钒钛磁铁矿的冶炼工艺比较
2020-04-27 作者:佚名 网友评论 0 条
武汉科思瑞迪科技有限公司
钒钛磁铁矿是一种铁、钒、钛等多种有价元素共生的复合矿。我国钒钛磁铁矿资源主要分布在四川的攀枝花—西昌地区和河北的承德地区。围绕钒钛磁铁矿资源的综合利用,我国的冶金工作者开展了诸多的研究和实践工作。针对钒钛磁铁矿的处理工艺,按照冶炼方式的不同,可分为两类:高炉冶炼工艺和非高炉冶炼工艺。
1 高炉冶炼工艺
目前,采用高炉冶炼工艺处理钒钛磁铁矿的主要有中国的攀钢和承钢、俄罗斯的丘索夫钢铁公司和下塔吉尔钢铁公司,基本工艺流程如图1所示。
高炉冶炼工艺具有技术成熟可靠、生产效率高、且能够实现钒钛磁铁矿的规模化利用等诸多优点。由于高炉冶炼工艺需要合适的炉渣粘度以确保炉内透气性和炉渣流动性,入炉原料中通常要配入30%左右的普通铁矿,所形成的高炉渣中TiO2的含量通常不超过20~25%,这种高钛型高炉渣的提钛工艺技术难度较大,目前尚无有效的利用技术;因此,高炉冶炼工艺只利用了钒钛磁铁矿中的铁和钒资源,而高炉冶炼工艺,钒钛磁铁矿中的钒被还原进入铁水,然后在提钒转炉中进行吹氧提钒获得钒渣,最终获得的钒渣中钒的综合收得率通常不高于60%,亦有相当数量的钒未被有效回收。
此外,高炉冶炼工艺的系统及装备配置复杂、工序能耗高、污染物排放量大,在践行绿色发展、推进生态文明建设的时代背景下,高炉冶炼工艺面临较大的环保和资源压力
2 非高炉冶炼工艺
目前,采用非高炉冶炼工艺处理钒钛磁铁矿的成熟技术,主要是回转窑直接还原-电炉熔分工艺。我国在非高炉冶炼工艺处理钒钛磁铁矿方面,进行了大量的研究和实践工作,并取得了一定的进展和突破。
2.1 回转窑直接还原-电炉熔分工艺
目前,采用回转窑直接还原-电炉熔分工艺处理钒钛磁铁矿的主要有新西兰钢铁公司和南非海威尔德钢钒公司,基本工艺流程如图2所示。
回转窑直接还原-电炉熔分工艺具有技术成熟、污染物排放量少、系统及装备配置简单、可实现100%钒钛磁铁矿入炉等优点;此外,回转窑预热预还原工艺可直接采用粉矿入炉,回转窑处理后的物料可直接热装进入电炉,从而实现物料高温物理显热的有效回收利用。通过回转窑直接还原后得到的直接还原铁,在电炉中进行深度还原和熔分,获得含钒铁水和熔分钛渣;含钒铁水在铁水包中进行吹氧提钒,从而获得钒渣,最终获得的钒渣中钒的综合收得率通常为70~80%。由于经回转窑处理后的物料既含有直接还原铁,也含有过剩的还原剂,在电炉熔分过程中,还原剂中的灰分进入渣相,从而稀释了熔分钛渣中TiO2的含量,因此,本工艺的熔分钛渣中TiO2含量在30~35%,目前亦未得到有效利用。
此外,采用回转窑作为直接还原设备,回转窑炉内物料通过高温火焰和烟气进行加热,炉内氧化性气氛和还原性气氛无法有效隔离,炉内物料依靠窑体的转动而实现迁移;由于该工艺的先天不足,导致产品质量不稳定、能源消耗过高;另外,由于窑体内部易于发生结圈故障,设备作业率通常偏低。
采用回转窑作为直接还原设备,单台套设备的最大产能规模一般不超过20万吨/年,因此,当物料处理量较大时,需要配备多条回转窑生产线;此外,由于回转窑排出物料中铁的金属化率通常不超过80%,导致电炉冶炼工序承担熔分功能的同时还承担较重的还原任务,因此电炉冶炼的电能消耗较高。
2.2 转底炉直接还原-电炉熔分工艺
我国的龙蟒集团和攀钢进行了转底炉直接还原-电炉熔分工艺处理钒钛磁铁矿的工业试验研究工作,积累了一定的实践经验。基本工艺流程如图3所示。
转底炉直接还原工艺可以100%采用钒钛磁铁矿,具有系统及装备配置简单、污染物排放量较少等优点;转底炉排出的物料通过热装进入电炉,可以有效回收高温物料的物理显热。在电炉熔分工序,通过深度还原和熔分,分别得到含钒铁水和熔分钛渣,含钒铁水进一步吹氧提钒,从而获得钒渣,最终获得的钒渣中钒的综合收得率通常为不低于75%。由于转底炉采用内配碳球团作为入炉原料,还原剂中的灰分残留在直接还原铁内,经电炉熔分后进入渣相,对熔分钛渣中TiO2的含量具有一定的稀释效应。
转底炉内物料通过高温火焰辐射和对流的方式对物料进行加热,由于转底炉旋转一周的时间通常为20~30min,为了确保铁氧化物的还原率,炉膛温度通常高达1300~1350℃,导致炉底易于发生板结,影响设备作业率;而直接还原铁的金属化率较低,通常不超过75%,这也使得电炉冶炼工序承担熔分功能的同时还承担较重的还原任务,因此电炉冶炼的电能消耗较高。
另外,由于转底炉的运转需要庞大的驱动机构,单台套设备的最大产能规模一般不超过30万吨/年,因此,采用转底炉作为直接还原设备时,规模化生产能力的提升将会受到制约。
2.3 COSRED直接还原-电炉熔分工艺
武汉科思瑞迪科技有限公司的发明专利(2016年获国家授权):COSRED直接还原-电炉熔分工艺,基本工艺流程如图4所示。
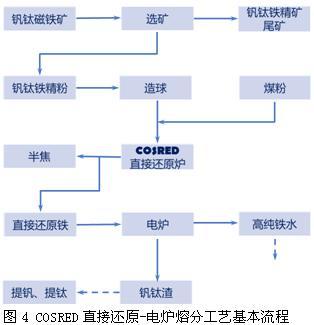
COSRED直接还原-电炉熔分工艺与前述工艺最大的不同在于:前述工艺均需将钒钛磁铁矿中的钒还原进入铁水,然后通过吹氧提钒获得钒渣;而COSRED直接还原-电炉熔分工艺,则是在电炉熔分后直接获得钒渣,省去了钒氧化物的还原和再氧化环节。
COSRED直接还原工艺可以采用100%的钒钛磁铁矿作为入炉原料,由于还原炉内的还原气氛和氧化气氛完全隔离,因此,直接还原铁的金属化率能够稳定的达到90%以上,电炉的功能主要是对入炉的直接还原铁进行熔分,无需承担额外的还原任务,电炉的熔炼电耗较低;当采用直接还原铁热装进入电炉时,可进一步降低电耗;电炉熔分后直接获得高纯铁水和钒钛熔分渣,钒钛渣进一步用于提钒和提钛操作,从而实现钒钛磁铁矿中铁、钒、钛综合回收利用的效果。由于本工艺直接还原工序采用外配还原剂,直接还原铁的成分不受还原剂中的灰分的影响,因此,电炉熔分钛渣中TiO2的品位也不会受此干扰。不同的钒钛磁铁矿进行COSRED直接还原-电炉熔分的工业试验的生产实践表明,本工艺的铁、钒、钛的综合收得率均能达到95%以上。
此外,COSRED直接还原工艺可实现100万吨及以上的规模化生产能力,从而为采用非高炉冶炼工艺进行规模化处理钒钛磁铁矿提供了一种可行的解决方案。
3 工艺比较
对上述几种处理钒钛磁铁矿的工艺方法进行归纳比较,见表1。

4 结语
采用非高炉冶炼工艺处理钒钛磁铁矿,具有工艺流程短、冶炼操作简单、能源消耗和环境污染少等技术优势,是处理钒钛磁铁矿的理想工艺路线。COSRED直接还原工艺通过模块化组合可以实现100万吨及以上的规模化生产能力,为采用非高炉冶炼工艺进行规模化处理钒钛磁铁矿提供了一种解决方案。实践证明, COSRED直接还原-电炉熔分工艺处理钒钛磁铁矿的技术可行、运行可靠、优势突出,并且能够实现极高的铁、钒和钛的综合回收率,是钒钛磁铁矿综合利用的最佳工艺技术,具有巨大的推广价值和市场前景。
关注“driinfo",手机上同步看直接还原、钢铁业内文章
相关文章
[错误报告] [推荐] [收藏] [打印] [关闭] [返回顶部]