固态还原钛铁矿生产钛渣新技术
2020-06-08
庞建明
中国钢研科技集团有限公司资源应用与合金材料事业部
目前世界上90%以上的钛铁矿用于生产钛白,约4~5%的钛矿用于生产金属钛,其余钛矿用于制造电焊条、合金、碳化物、陶瓷、玻璃和化学品等。我国的钛资源储量非常丰富,但主要的钛铁矿,金红石矿甚少。我国钛矿主要由广东、广西、海南、云南和四川攀枝花开采生产,主要产品是钛铁矿精矿,也有少量的金红石精矿。由于钛铁矿精矿的品位较低,通常经过富集处理获得高品位的富钛料¾高钛渣或人造金红石,才能进行下一步的处理。
电炉熔炼法是一种成熟的方法,工艺比较简单,副产品金属铁可以直接利用,电炉煤气可以回收利用,三废较少,工厂占地面积小,是一种比较高效的冶炼方法[1-3]。电炉熔炼法可得到TiO2含量为80%左右的高钛渣,作为下一步处理(如酸浸法或氯化法)的原料。
由于电炉熔炼法属于高温冶金,能耗高是其固有的特点,生产1吨高钛渣,大约需要3000kWh的电能,而实际上将铁从钛铁矿中还原出来所需的化学能量仅在500kWh左右,即能量的有效利用率仅在17%左右,非常低;其二、电炉熔炼法使用冶金焦或石油焦作还原剂,也存在一定的环境污染。
针对钛铁矿的特殊性能,作者历时多年研究,在2005年提出了固态还原冶炼钛铁矿新工艺[4],该工艺将钛铁矿和碳质还原剂(如煤粉) 粉体的粒度磨细到10μm左右时,可在600℃左右实现快速还原反应将铁还原出来,冷却后通过磁选分离方式得到高钛渣和铁粉。在此研究基础上,作者又经过6年研究,提出了钛铁矿固态还原与晶粒长大技术,从而提高铁与高钛渣(或酸渣)的分离效率。
本文将介绍作者在钛铁矿固态还原领域研究的最新理论及技术成果。
1固态还原钛铁矿生产钛渣的理论
1.1 钛铁矿还原热力学研究
钛铁矿中主物相是FeTiO3,伴有少量Fe3O4、SiO2、MgO、CaO等物相。还原的目标是将矿中的氧化铁还原成金属铁再分离。
碳与FeTiO3的主要反应为[5,6]:

从图2可见,碳的气化反应(C+CO2=CO)与FeTiO3间接还原的曲线的交点为A,温度大约800℃,表明在800℃以上碳在热力学上是能够还原FeTiO3的。
钛铁矿中的磁铁矿Fe3O4相对比较容易还原,一般遵循逐步还原原理[6-9],即先从Fe3O4还原到FeO,然后从FeO还原到金属铁,比较难还原的阶段是从FeO到金属铁,其与碳的反应式如下:

碳的气化反应(C+CO2=CO)与FeO间接还原的曲线的交点为B,温度大约700℃,表明在700℃以上碳在热力学上是能够还原FeO的。对比A、B两点位置可以发现,FeTiO3比FeO难还原,还原的温度大致要高100℃。从FeTiO3、FeO与CO反应曲线可见,平衡成分中,FeTiO3与CO还原需要更高的还原势(更高的CO浓度)。
随着反应的温度提高,从FeTiO3还原出来的TiO2有可能进一步被还原成Ti3O5[5,6],其反应式如下:

碳的气化反应(C+CO2=CO)与TiO2间接还原的曲线的交点为C点,温度大约1000℃,表明在1000℃以上碳在热力学上是能够还原TiO2的。对比A、B、C三点位置可以发现,TiO2还原是最为困难的。从TiO2、FeTiO3、FeO与CO反应曲线可见,平衡成分中,TiO2与CO还原需要更高的还原势(更高的CO浓度,几乎99%CO),但随着反应温度的进一步提高,还原势浓度有所下降。
随着反应温度的提高Ti3O5还能进一步被碳还原成Ti2O3、TiO等含钛氧物相[5,6]。

在正常的电炉冶炼过程中,TiO2很容易被还原到Ti3O5与Ti2O3,在温度低于1300℃下还原,TiO2有可能被还原到Ti3O5,若使用低温冶炼,TiO2很可能不被还原到低价状态。
1.2 钛铁矿固态还原动力学研究
将不同粒度的钛铁矿与一定比例焦粉(固定碳83%)混匀后在1100℃加热还原,得到的结果见图3。正常粒度的钛铁矿粉(200微米)还原速度是比较慢的,还原3个小时,铁的还原率才达到50%水平,将矿粉的粒度磨细到50微米水平,两个小时的还原率达到75%,如果将矿粉的粒度磨细到20微米水平,还原两个小时的还原率可以接近90%水平。如果将粒度进一步磨细,反应速度还会进行加快[4]。
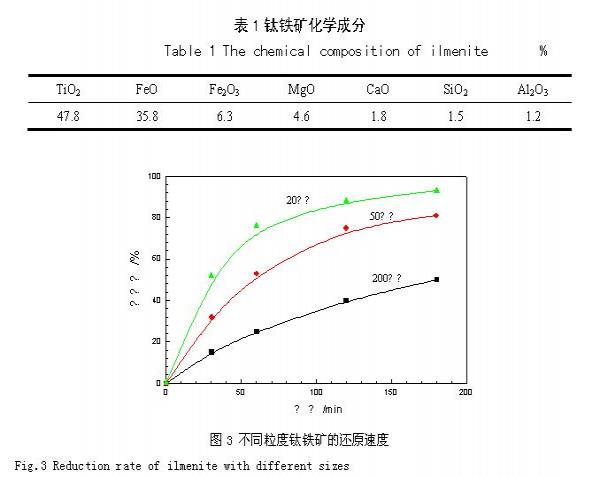
1.3 钛铁矿铁晶粒长大分离理论及试验
钛铁矿还原以后最大的困难是铁从含钛渣中的分离,正常遇到的困难是铁很难从含钛渣中分离完全,导致部分铁残留在钛渣中以及部分含钛渣留在铁粉中。由于钛渣冶炼的含钛渣以及铁都是产品,这种分离不彻底,会导致两种产品的质量都受到影响。
另一种方法是进行高温熔分,将还原后的产品进入高温电炉,利用高温将炉渣及铁熔化来实现渣铁分离。诸多研究表明,通过预还原+电炉熔分的效果较差,一是使工艺复杂化,顺行困难;二是能耗较高。
为了提高渣铁分离效率,作者提出了晶粒长大分离理论,将还原后的炉料在一定温度(1200℃~1300℃)下保温40min~80min,促使铁晶粒长大,达到可分离条件。通过适当的添加剂以及工艺制度,完全可以使铁晶粒的粒度长大到100微米,在某些条件下还可形成厘米级的铁粒(见图6)。这样通过简单的磁选即可得到纯净的铁产品以及高钛渣(或酸渣,与钛铁矿成分相关)。
2 钛铁矿固态还原与晶粒长大新技术
根据上述理论研究成果,作者开发了钛铁矿固态还原与晶粒长大新技术。新技术的工艺流程是:首先将钛铁矿粉、还原剂和添加剂在高效球磨机中磨细,然后按照一定的比例混合,放入压球机中压制成球,将球团干燥后,放入固态还原反应器内加热、还原,还原后的物料在晶粒长大反应器内完成铁粒长大,冷却后破碎,通过磁选方式完成钛渣与铁粒分离。

新技术最大的优势是降低了反应温度,不需要高温还原与熔分即可得到铁产品及钛渣产品,无需电炉熔炼,是一种钛铁矿资源与能源高效利用的新工艺。具体表现在:
(1)能耗低
固态还原工艺的最主要特点是降低冶炼能耗:由于冶炼温度低,物料的物理热量仅为0.9GJ/t高钛渣(240kWh/t高钛渣),仅相当于电炉熔炼法的1/4~1/3左右;其次,化学反应较单一(仅有铁的还原),而TiO2的还原等副反应(如TiO2→Ti3O5→Ti2O3)难以发生,因此化学反应耗热少(500 kWh/t高钛渣),约为电炉熔炼法的60%左右;再次,低温条件下,尾气、冷却水带走的热量也仅相当于电炉熔炼法的1/3左右。因此,低温法冶炼高钛渣的能量约为1100kWh/t高钛渣,相当于电炉熔炼法的1/3左右。
(2) 冶炼方法灵活
固态还原工艺除了可以用电加热外,还可采用煤或气作为热源。还原剂的选择可根据钛铁矿的成分而定,如果钛铁矿中全Fe含量高、而脉石(MgO、SiO2、Al2O3等)杂质含量低,通过还原可以得到TiO2含量为90%以上的高钛渣,则可选用较纯的碳质还原剂(如碳粉等)。若钛铁矿中脉石含量高,通过还原可以得到TiO2含量为80%左右的高钛渣,则可选用低灰份的煤粉作为还原剂。
(3) 环保友好
低温冶炼法可用煤作为还原剂,而不需要焦炭或石油焦作为还原剂,避免了冶炼焦炭或石油焦过程的环境污染。低温下NOx、SOx等有害气体难以形成,因此排放量远低于电炉熔炼法的排放量。低温下,冷却水的用量也要明显少于电炉熔炼法的用量。
3固态还原钛铁矿生产钛渣新技术放大试验
在研制的固态还原与晶粒长大反应器内进行了固态还原钛铁矿生产钛渣试验。试验步骤如下:首先将钛铁矿、煤粉、添加剂在高效球磨机中磨细,然后按照10:1.2:1的比例混合,放入压球机中压制成长度为50mm左右的椭圆球团,将压好的混合球团放入干燥设备中干燥,使混合球团中的物理含水量小于2%,然后将样品放入固态还原反应器内加热与还原,还原温度为1100℃左右,加热还原时间为1h30min。还原后的球团在高温下进入铁晶粒长大反应器中,在1250℃下促使晶粒长大到1mm以上,铁晶粒长大时间为30min。将晶粒长大后的产品冷却到200℃以下,送入破碎设备进行简单的破碎,然后送入磁选机进行磁选,完成钛渣与铁粒分离,最后产品为酸性钛渣和粒铁。
部分试验设备照片见图5。试验过程中钛铁矿一次性装料量为200kg,整个试验中未出现结疤现象。使用的钛铁矿化学成分见表1。通过固态还原与晶粒长大方法,得到了铁粒与含钛炉渣,其化学成分见表2与表3。粒铁的照片见图6。可见,通过钛铁矿固态还原冶炼与晶粒长大新技术,可以成功得到酸性钛渣与粒铁,下一步将进行更大规模的连续性工业试验。

4结论
本文研究了钛铁矿固态还原理论,在此基础上开发出了固态还原钛铁矿生产钛渣技术。主要结论如下:
(1)还原热力学表明,钛铁矿的还原难度高于普通的铁矿。
(2)动力学研究表明,通过粉体细化,可以加速钛铁矿的还原速度。
(3)通过晶粒长大技术将还原后的铁晶粒长大到一定粒度,通过简单磁选,即可得到铁产品和钛渣。
(4)开发的钛铁矿固态还原与晶粒长大新工艺流程为:首先将钛铁矿、还原剂和添加剂在高效球磨机中磨细,然后按照一定的比例混合,放入压球机中压制成球,将球团干燥后,放入固态还原反应器内加热、还原,还原后的物料在晶粒长大反应器内完成铁粒长大,冷却后破碎,通过磁选方式完成钛渣与铁粒分离。
(5)钛铁矿固态还原与晶粒长大新工艺具有反应温度低、无需高温熔分等特点,从而实现高效率、低能耗及低成本生产钛渣和铁产品。
相关文章
[错误报告] [推荐] [收藏] [打印] [关闭] [返回顶部]