HIsmelt工艺冶炼钒钛磁铁矿工业试验
2021-10-21
曹朝真1,2,张函冠3,王金霞4,张笑然3,
陈庆恒3,王林顺4,李成峰3,张冠琪4
1.北京首钢国际工程技术有限公司2.北京市冶金三维仿真设计工程技术研究中心
3. 承德信通首承科技有限责任公司4. 山东墨龙石油机械股份有限公司
钒钛磁铁矿是一种典型的多金属伴生矿,具有极高的综合利用价值,但由于其贫、细、散、杂的特殊性,给其冶炼带来了一定困难,目前,对于钒钛磁铁矿的冶炼主要以高炉流程为主。在高炉冶炼钒钛矿生产过程中,在高炉内的高还原势和高温条件下,钛的氧化物会被部分还原并生成高熔点的TiN和TiC,这些高熔点的物质会引起炉渣变稠,严重时造成出渣和渣铁分离困难;此外,由于还原反应生成更多气体以及钒钛渣的发泡特性,造成高炉冶炼钒钛矿易出现泡沫渣,使高炉下部透气性恶化,从而影响正常生产[1-3]。
与高炉工艺不同,HIsmelt工艺炉内没有固体料柱,同时由于采用较高的二次燃烧率,使得SRV炉内熔渣的氧势与高炉相比显著提高,这一根本性的技术特征使得HIsmelt工艺在冶炼钒钛矿时,渣中的TiO2不会被过度还原形成高熔点物质,从而使得炉渣能够保持较好的流动性,有利于冶炼过程的稳定进行。国内首座年产80万吨铁水的墨龙HIsmelt工厂已于2016年建成投产[4],通过4年多的工业生产实践和工艺改进,各项技术经济指标和运行稳定性显著提高[5],为开展HIsmelt工业试验奠定了基础。以首承钒钛矿为原料,在墨龙HIsmelt熔融还原炉上进行了首次100%钒钛磁铁矿冶炼工业试验,研究了SRV炉冶炼钒钛磁铁矿适宜的工艺参数和冶炼规律,为HIsmelt工艺冶炼钒钛矿进行了工业化探索。
1试验原料
本次试验以首承钒钛磁铁矿氧化球团为原料,经破碎后获得6mm以下粉料,用作SRV炉喷吹含铁原料,含铁粉料的粒度原则应满足-0.1mm<10%和+4mm<10%。试验配矿用铁矿粉采用PB粉,喷吹煤和熔剂均采用墨龙现场原料。首承钒钛磁铁矿和PB粉主要化学成分见表1。

由表1可以看到,首承钒钛球粉TiO2含量相对较低为2.33%,属于低钛型钒钛磁铁矿,S和P含量较低,Cr含量偏高。
2试验方法
试验分阶段进行,钒钛磁铁矿的初始配入量为40%,炉内物料置换完全后,按照60%、80%、100%依次增加钒钛矿配比。试验初始阶段,炉渣二元碱度控制在1.1-1.25,Mg/Al=0.5-0.6,试验过程中,根据渣铁成份、泡沫渣、炉内燃烧、炉体热负荷、煤气成份及温度波动等情况,判断是否进入下一阶段。试验期间取渣样、铁样和煤气灰样进行快速分析,并做好记录。试验选取临近日期且SRV炉平稳运行的生产数据作为基准期数据。
3试验结果及分析
3.1试验过程及结果
本次试验过程共分为四个阶段,具体过程见表2。

1-1阶段试验从3月2日8:00开始至3月3日8:00结束,冶炼过程中,固定钒钛矿配比为40%,喷煤量为69.5t/h,R2=1.2,渣中MgO=9-10%,热风量为15万Nm3/h,初始喷矿量为130t/h,通过调节喷矿量来调节炉况。试验过程中,炉况整体情况稳定,冶炼正常。渣中FeO%偏高约为10%,渣中TiO2%最高达到3.8%,渣中V2O5%最高为0.38%;试验过程中为维持合理的二次燃烧率,喷矿量由130t/h逐步降低至115t/h,受喷矿量减少影响,炉渣温度稳步由1410℃升高至1440℃, 煤气热值有所升高。铁水温度基本控制在1380-1400℃,铁水C%由4.0%左右升至4.1%;出渣情况良好,渣量大,流动性好。
2-1阶段试验从3月3日8:00开始至3月3日21:00结束,在1-1阶段试验的基础上,钒钛矿配比提高至60%,其他条件不变。试验过程中,根据炉内情况喷矿量迅速由130t/h降为115t/h,渣中FeO%维持在10%左右,渣中TiO2%最高至5.55%,渣中V2O5%升高至0.45%,炉渣温度进一步由1440℃升高至1460℃,铁水温度有所降低,控制在1370-1380℃,铁水C%由4.1%最高升至4.18%;铁水中Cr%、V%逐步升高,60%钒钛矿物料入炉3小时开始,炉渣出现泡沫渣迹象。
2-2阶段试验从3月5日6:00开始至3月5日18:00结束,鉴于2-1阶段试验后期出现泡沫渣现象,在恢复炉况后,重新开始钒钛矿配比60%试验,初始喷矿量为130t/h,其他条件不变。本阶段试验过程与2-1阶段情况相似,渣中FeO前期逐步升高,降矿后,明显降低至8.6%,渣中TiO2%最高至5.57%,渣中V2O5%升高至0.4%,钒钛矿入炉一段时间后,煤气热值逐步提升,二次燃烧率开始逐步降低,为维持合理炉况,喷矿量由130t/h逐步降低至115t/h,试验过程中,渣量大,并始终具有较好的流动性,出现较明显泡沫渣。
3-1阶段试验从3月8日6:00开始至3月9日11:00结束,为了降低泡沫渣的影响,本阶段试验初始喷矿量固定为100t/h,钒钛矿配比固定为100%,同时喷煤量和热风量均相应下调。100%钒钛矿物料入炉后,渣中FeO%逐步升至10.2%,后降低至7-8%并保持平稳,提高喷矿量后有所提高,渣中TiO2%最高至7.75%,渣中V2O5%升高至0.55%,Ti和V在渣和铁水间的分配系数分别为492和5.3;出渣过程基本正常,未出现明显泡沫渣,逐步提高喷矿量至115t/h后,炉况波动有所加剧,有少量泡沫渣,但在可控范围内。
3.2试验结果分析
3.2.1炉渣FeO含量升高原因分析
本次工业试验结果表明,全钒钛矿冶炼时渣中FeO含量约为7-9%,与普通矿冶炼相比约升高2-3个百分点。由于试验过程中使用的喷吹煤及其它原料与冶炼普通矿时相同,而且试验时吨铁喷煤量较普通矿冶炼时有所提高,因此造成渣中FeO含量升高的原因应与钒钛矿本身的特性有关。

对两种矿粉的粒度分布进行了对比。由图1可以看出,钒钛矿粉呈深灰色,半球颗粒中掺杂部分细粉,与PB粉相比,目测其大颗粒和超细粉占比偏多。为此对上述两种矿粉的粒度进行炉检测,结果见图2。

Fig. 2 Comparison of particle size distribution between V-Ti magnetite and PB concentrate
由图2可以看出,粒径≥0.85mm的矿粉颗粒占比中,钒钛矿粉要明显高于PB粉,而粒径在0.85mm以下的矿粉颗粒占比则相反,可见,整体上钒钛矿粉的平均粒径要大于PB粉。矿粉粒度增大会延长矿粉在炉内的还原时间,导致渣中FeO含量有所升高。除此之外,矿粉的还原性差异也会对渣中FeO含量带来显著影响。
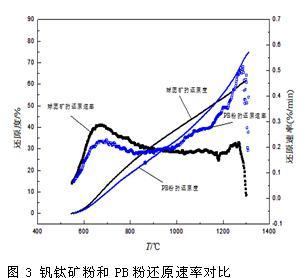
Fig. 3 Comparison of reduction rate between V-Ti magnetite and PB concentrate
图3为钒钛矿粉和PB粉煤粉还原实验结果对比图。从实验结果可知,在900℃以下,钒钛矿粉的还原速率略高于PB粉,二者差别不大;随着反应温度的升高,钒钛矿粉的还原速度呈缓慢降低的趋势,在900℃至1200℃区间内,还原速率基本保持不变,PB粉的还原速率在1000℃以上迅速升高,且远大于钒钛矿粉。对比认为,钒钛矿粉还原性差是造成渣中FeO含量的主要原因之一。
3.2.2炉渣特性分析
表4为全钒钛矿冶炼时水渣的主要化学成份,渣中TiO2含量为7.08,属于低钛渣。

图4为全钒钛矿冶炼时SRV炉干渣的XRD图谱,从图中可以看出,炉渣干渣物相成份主要以Ca2(Mg0.75Al0.25)(Si1.75Al0.25O7)、MgAl2O4、CaTiO3、Fe3O4等为主,其中TiO2主要以钙钛矿形式存在。传统的高炉水渣是重要的矿渣水泥原料,渣中TiO2含量增加会对炉渣活性带来不利影响,为了检测全钒钛矿冶炼时,含钛水渣的活性,对不同含钛水渣配比的水泥活性进行了检测。从表5检测结果可以看出,随着水渣配比升高,水泥7天活性指数显著降低,水渣配比为50%时,水泥7天活性指数为47,按照不同标号水泥对活性指数的要求,含钛SRV水渣在实际使用时其配加量相较于普通高炉渣会有所降低。
3.2.3钒、钛在渣铁间分配规律

Fig. 5 Distribution ratio of V between slag and hot metal
图5为试验期间各阶段钒在渣铁中的分配比变化图。由图中可知,随着钒钛矿粉配入量的增加,进入铁水中的钒的比例逐步升高,全钒钛矿冶炼时,钒在渣铁中的分配比约为5.3,与1-1阶段相比,降低约72%。钒在渣铁中分配比的提高与煤比增加有关,过量的煤粉使得炉内的还原势相对增强,从而使更多的钒被还原进入铁水。

图6 钛在渣铁中的分配比
Fig. 6 Distribution ratio of Ti between slag and hot metal
图6为试验期间各阶段钛在渣铁中的分配比变化图。试验期间,随着钒钛矿粉配入量的增加,(Ti)含量逐步升高,但[Ti]含量相对稳定,全钒钛矿冶炼时,钛在渣铁中的分配比约为492。
3.2.4泡沫渣的生成原因分析
……
关注“driinfo",手机上同步看直接还原、钢铁业内文章
相关文章
[错误报告] [推荐] [收藏] [打印] [关闭] [返回顶部]