纯氢竖炉还原及高纯材料制备工艺技术开发
2022-09-28
周和敏,郝晓东,杨光浩,张俊,沈朋飞,徐洪军,何鹏
中国钢研科技集团有限公司氢冶金(绿色冶金)中心
引言
气候变化是人类面临的全球性问题,随着各国CO2排放量持续增加,对全球生态系统形成威胁。钢铁生产是典型的铁-煤化工过程,钢铁行业作为工业的重要领域,是能源消费大户,同时也是CO2排放大户。据世界钢铁协会数据统计,2020年全球钢铁行业吨钢CO2排放平均值为1.85t/t,全球钢铁行业的直接碳排放总量约为26亿t,CO2排放总量约占全球化石燃料燃烧产生的CO2直接排放总量的7~9%。我国钢铁工业CO2排放总量在2014年出现了拐点,达到排放量最高峰17.31亿t,随后开始呈现下降态势。而近年来由于粗钢产量猛增,特别是2019年粗钢产量达到了9.95亿t,我国钢铁工业CO2排放总量又上升到16.25亿t左右。2020年粗钢产量更是达到了10.65亿t,初步估算其对应的CO2排放总量为17.38亿t左右。我国高炉炼铁-转炉长流程钢产量约占90%左右,铁前工序能耗占总能耗约70%,CO2排放铁前占73.1%,参见表1所示。我国吨钢CO2排放与国际先进的长流程企业比较接近。吨钢CO2排放量在1.8~2.0吨之间,吨铁CO2排放量在1.4~1.5吨之间。因此,减少铁前CO2排放量,才是实现钢铁行业“碳达峰、碳中和”的关键。
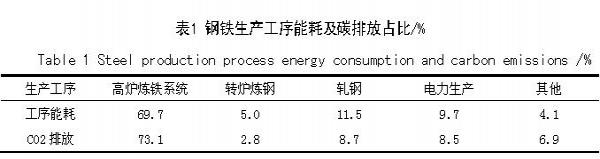
氢气作为能源和还原剂的产物均为水,不会产生任何污染物排放。纯氢还原炼铁是解决实现我国钢铁行业“碳达峰、碳中和”的根本解决方案之一。
1 纯氢冶金技术路线
1.1可再生能源对氢冶金的影响
中国的风能和太阳能发展了将近40年的发展,取得非常大的成绩。全国发电装机容量24亿kw,其中风电2.99亿kw,太阳能2.82亿,水电3.85亿kw,可再生能源总装机超过10亿kw。2020年中国发电量约为7.14万亿kwh,其中可再生能源发电量为2.215万亿kwh。尽管风能、太阳能增量巨大,可与煤电相比仍然相当有限。以2019年为例,全国的风能和太阳能加起来发电总量相当于约1.92亿吨标准煤的发电量,也就是说,上网的风能和太阳能发电总量大约只能取代煤炭发电的12.5%左右。目前国内弃光弃风的问题非常严重,因为电网只能容纳~15%的非稳定电源,风能、太阳能发出来的电,电网没法全部承受。通过太阳能、风能、生物质能电解水制备绿氢和氧气成本上在碳中和的背景下是有竞争力的,可以大力发展太阳能、风能减碳产业。国家发展改革委、国家能源局联合研究制定了《氢能产业发展中长期规划(2021—2035年)》,在“十四五”时期,我国将初步建立以工业副产氢和可再生能源制氢就近利用为主的氢能供应体系,风电、光伏发电度电成本将进一步下降。据中国可再生能源学会介绍,过去10年,我国陆上风电度电成本下降了约40%。目前西北风能资源好的地区,成本大概为0.3元/千瓦时(个别地区甚至0.2元/千瓦时以内),中东部和南方地区成本为0.4元/千瓦时。数据显示,2020年我国陆上风电、光伏发电平均度电成本分别降至0.38元和0.36元左右,同比分别下降10%和18%,风电行业力争在2025年将陆上高、中、低风速地区的度电成本分别降至0.1元、0.2元和0.3元,将近海和深远海风电度电成本分別降至0.4元和0.5元。在相关国家政策的驱动下,为下一步高比例、低成本、大规模发展绿氢冶金创造了有利条件。
1.2 氢还原的特性
所谓氢冶金就是在还原冶炼过程中主要使用氢气作还原剂。氢是最活泼的还原剂,在铁氧化物的气-固还原反应过程中,提高气体还原剂中氢气的比例,可以明显提高其还原速率和还原效率。与一氧化碳的还原潜能相比,氢气的还原潜能大大高于一氧化碳。采用氢气作为还原剂,氢冶金的还原效率和速率远高于碳冶金,铁矿石在固态条件下直接还原为铁,可以作为冶炼优质钢、特殊钢的纯净原料,也可作为铸造、铁合金、粉末冶金等领域含铁原料。因为不使用焦炭炼铁,原料使用氧化球团或冷压球团,不用烧结矿,所以氢冶金是一种优质、低耗、近零污染、无碳冶金的颠覆性新工艺,是全世界公认的最清洁环保冶金技术,有利于强化行业绿色发展理念,提升绿色制造水平,彻底实现产业升级。
(1)传统的高炉炼铁是用焦炭不完全燃烧产生的CO作还原剂,而氢冶金是以高化学能氢作还原剂,还原剂的改变引发了冶金流程效能的根本性变化。从反应机理推算,H2的还原潜能是CO的11倍。由于H2的分子直径小,在铁矿石中的穿透能力是CO的5倍,大大提高了反应速度,降低了反应温度,铁矿石不经过相变,可直接还原成纯铁。
因此,高炉使用氢气作还原剂理论上可以实现快速还原。氢还原是吸热反应,如果高炉里氢含量增加,高炉内就会热量不足,如何防止热量不足是氢还原的关键。在氢还原中,随着铁矿石还原会发生粉化现象,使高炉内气体通路不畅,因此需要研究防止高炉透气性不良的对策。
(2)碳冶金反应Fe2O3+3CO=2Fe+3CO2,氢冶金反应Fe2O3+3H2=2Fe+3H2O,由碳冶金转向氢冶金是钢铁工艺流程巨大的变化。碳冶金的最终产物是CO2,钢铁工业CO2排放占全国CO2总排放量的14~15%左右,高炉炼铁CO2排放为73.1%,而氢冶金的还原剂为H2,最终产物是H2O,真正做到了CO2零排放,所以将碳冶金转变为氢冶金是钢铁工业发展低碳经济的最佳选择。
(3)氢冶金在冶金过程中不与焦炭接触,生产的DRI为高纯铁,产品质量高,有利于电炉生产出高纯净钢。以氢还原过程生产的高纯海绵铁作为主要原料进行钢水超纯精炼的过程,不同于传统碳饱和铁水的脱碳、钢水脱氧和内生夹杂物上浮去除过程。超洁净海绵铁的熔化温度高,如何在有效保护条件下完成其快速熔化和渣铁分离,实现成品钢水的超洁净化,是该技术路线的主要技术精髓之一。
1.3 制氢技术路线比较
1.3.1 水电解制氢技术
通过直接电解纯水产生高纯氢气,电解池只电解纯水即可产氢。通电后,电解池阴极产氢气(氢气纯度≥99.8%),阳极产氧气(氧气纯度≥99.8%),氢气进入氢/水分离器,即可获得高纯氢气和氧气。
水电解制氢系统的工作原理是由浸没在电解液中的一对电极中间隔以防止气体渗透的隔膜而构成的水电解池,当通以一定的直流电时,水就发生分解,在阴极析出氢气,阳极析出氧气。其反应式如下:
阴极:2H2O + 2e → H2↑+ 2OH-
阳极:2OH- - 2e → H2O + 1/2O2↑
总反应:2H2O → 2H2↑+ O2↑
氢气进入干燥器除湿后,经稳压阀、调节阀调整到额定压力(0.02~0.45Mpa可调)由出口输出。电解池的产氢压力由传感器控制在0.45Mpa左右,当压力达到设定值时,电解池电源供应切断;压力下降,低于设定值时电源恢复供电。水电解制氢电耗≤4.6KWh/ m3H2。水电解制氢参见图1所示。

该技术的优点是工艺简单、原料不受限制、无污染、氢气品质高,但目前无法大规模应用的唯一缺点在于电解成本高,而成本主要取决于电价。火电在相当长的一段时期内无法解决成本问题,也不环保。采用绿电就地制氢将是未来氢冶金发展的方向,但目前涉及储存和输送相关技术难题。
1.3.2 天然气制氢技术
在所有气基DRI工艺中,以天然气为能源的竖炉法生产直接还原铁占世界总产量的80%以上。但是,中国常规天然气资源相对贫乏,2021年中国天然气的对外依存度达45%,天然气消费3726亿m3,进口量达1675亿m3,而且购气成本还在不断升高,以常规天然气为能源的气基直接还原技术在中国发展前景受到限制。
以天然气为原料蒸汽转化制氢工艺,参见图2所示。为了满足转化催化剂对硫含量的要求,需要对原料气进行精脱硫,精脱硫后原料气中总硫含量控制在0.2ppm以下。精脱硫可采用加氢转化有机硫+氧化锌脱硫剂吸收转化生成H2S的方案。
蒸汽转化通常采用传统的顶烧式方箱型结构。转化管在辐射段方箱内成排直立布置,每排转化管之间设顶部烧嘴,通过燃料气的燃烧以辐射传热方式为主为转化管内的反应物料提供烃类蒸汽转化所需的热量。
其主要反应如下:2CnH2n+2+nH2O=nCH4+nCO+(n+2)H2
CnH2n+2+nH2O=nCO+(3n+1)H2
CH4+H2O=CO+3H2
CO+H2O=H2+CO2
转化炉的对流段是余热回收段,辐射段烟道气从辐射段下部侧面出来后即进入对流段。在对流段中,烟道气沿水平方向流动,换热盘管根据加热要求和传热特性按混合气预热器、原料气预热器、烟气蒸汽发生器、空气预热器等顺序合理排列,以使烟道气热量得到充分的回收利用。烟道气最终温度降至~150℃左右经引风机送烟囱放空。
PSA脱碳脱水提氢可用变压吸附方法将转化气中的H2、CO、CH4与还原气分离提纯,得到产品氢气。吸附解吸气中含有H2、CO、CH4,绝大部分返回炉子作为补充燃料用,烟道气最后通过烟囱排放,无大气污染问题。氢气制备需要原料天然气约0.315m3/m3H2。

1.3.3 焦炉煤气制氢技术
焦炉煤气是焦化厂的副产物,一般H2含量高于60%,CH4含量高于20%,其余成分为CO、CO2、N2和CmHn。焦炉煤气制氢路线分为两种:一是重整后制备H2与CO的混合气,再通过变压吸附分离CO获取纯H2,解析气作为燃料利用;二是焦炉煤气直接变压吸附获取纯H2,解析气再通过深冷法分离CH4,或者直接作为燃料气利用。
(1)焦炉煤气重整后变压吸附
焦炉煤气重整包含三种方式,分别是自重整法、水蒸汽裂解法和CO2裂解法,流程图分别如图3、图4和图5所示。从流程图可知,不管采用何种重整工艺,重整气的温度均高于600℃,变压吸附之前需进行冷却和干燥处理,不仅降低了热处理效率,还延长了工艺流程,增加了设备投资。

相关文章
[错误报告] [推荐] [收藏] [打印] [关闭] [返回顶部]